X-Ray Imaging and Computed Tomography
- Imaging and Radiooncology

Prof. Dr. Marc Kachelrieß
X-ray computed tomography (CT), based on the measurement of x-ray attenuation from a multitude of view angles around the patient, is the workhorse of the radiologist. Since the introduction of CT in 1972, the importance of CT for the medical healthcare has increased dramatically. Major technical, mathematical, algorithmical and clinical improvements have taken place in the meantime over nearly four decades.
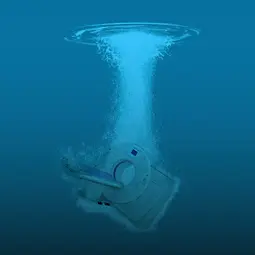
Our Research
Today, the most modern clinical scanners perform up to four rotations per second and thereby simultaneously acquire up to 320 slices that cover a 50 centimeter diameter field of measurement with a length of up to two meters. Complete patients can be assessed with CT in less than five seconds with an isotropic spatial resolution of down to 0.3 millimeters, with a temporal resolution as good as 70 milliseconds, and with image noise being less than 5% of the image contrast. Further on, dual energy CT allows assessing spectroscopic properties of the object, such as the exact quantification of iodine within muscle tissue or as the chemical composition of renal stone prior to treatment, for example. The spectrum of clinical CT applications is sophisticated and manifold. Typical applications are standard scans, whole body scans for trauma patients, cardiac CT, dual energy CT, dynamic CT, CT angiography, cardiac or coronary CT angiography, bone densitometry, lung screening, virtual colonoscopy, and many more.
Besides clinical computed tomography, several other medical CT modalities are in use, today. Interventional studies, for example, are often carried out under C-arm CT guidance, where a flat detector and a small x-ray source rotate around the patient. Oral and maxillofacial surgery, as well as the planning of dental implants, often relies on the so-called digital volume tomography (DVT), which is a dedicated flat detector CT system for the patient head. Radiation therapy even uses two CT modalities for image guidance: a clinical CT scan is used for planning, while the treatment unit itself is equipped with dedicated flat detector CT systems used for patient positioning and treatment verification. In the preclinical domain dedicated small animal CT systems are in use. They allow supporting longitudinal pharmaceutical studies that may aim at monitoring tumor response or the influence of other medication. Often, CT is used in multi-modality scenarios to add prior information to other modalities. Among those scenarios combinations of PET with CT or SPECT with CT are the most prominent ones in medical care.
The division “x-ray imaging and computed tomography” of the DKFZ aims at improving x-ray and CT imaging in all aspects, with a special focus on cancer detection and tumor characterization. While calibration, preprocessing and dose reduction applies to both, radiographic and tomographic imaging, sophisticated image reconstruction and artifact reduction techniques is our focus in CT research. This includes the development of new methods to perform real-time imaging simulta-neously with the radiation treatment, potentially combining the information obtained by the kV imager with the portal images obtained from the MV treatment beam, the development of new registration and reconstruction algorithms to compensate for patient motion, as well as the development of new multi-spectral imaging techniques to improve tumor diagnosis and to allow for quantitative tissue decomposition into the dominating chemical components. Further, some of our projects aim at translating and adapting methods, originally developed for CT, to other imaging modalities, such as MRI and PET.
Research Topics
• Artifact reduction
• Calibration of CT systems
• Cardiac CT
• Clinical CT
• Dental CT and dental x-ray imaging
• Design of CT systems
• Dose reduction
• Dual-energy CT
• Photon-counting CT
• High performance image reconstruction
• Image Guidance for Radiation Therapy
• Industrial CT
• Interventional CT
• Monte Carlo-based dose and scatter prediction
• Motion compensation for respiratory and cardiac CT, PET, and MR
• Sparse-data image reconstruction
• Perfusion CT
• Pre- and post-processing
• Preclinical CT
• Quantitative PET imaging
• Radar-based respiratory motion monitoring
• Tomographic image reconstruction and restoration
Team
-
Prof. Dr. Marc Kachelrieß
-
Tilmann Adrian
-
Maryam Assadi
-
Lara Bartnick
-
Jonathan Bollig
-
Elias Eulig
-
Andreas Heinkele
-
Lukas Hennemann
-
Moritz Herb
-
Anton Fritz Kabelac
-
Dr. Michael Knaup
-
Catherine Marie Knobloch
-
Gernot Kristof
-
Jan Magonov
-
Dr. Joscha Maier
-
Jovenpreet Mandair
-
Ricco Martin
-
Maya Metzger
-
Philipp Oelze
-
Jaime Pena Betancur
-
Dr. Stefan Sawall
-
Dr. Philip Trapp
-
Roman von Stritzky
-
Jöken Wucherpfennig
Award Winning Publications
(Moses & Sylvia Greenfield Award for the best scientific paper on imaging in Medical Physics in 2022)
Klein L, Liu C, Steidel J, Enzmann L, Knaup M, Sawall S, Maier A, Lell M, Maier J, Kachelrieß M.
(Moses & Sylvia Greenfield Award for the best scientific paper on imaging in Medical Physics in 2021)
Eulig E, Maier J, Knaup M, Bennett NR, Hörndler K, Wang AS, Kachelrieß M.
(Moses & Sylvia Greenfield Award for the best scientific paper on imaging in Medical Physics in 2016)
Ritschl L, Kuntz J, Fleischmann C, Kachelrieß M.
Recent Publications
Kabelac A, Eulig E, Maier J, Hammermann M, Knaup M, Kachelrieß M.
Maier J, Sawall S, Arheit M, Paysan P, Kachelrieß M.
Sawall S, Baader E, Trapp P, Kachelrieß M.
Eulig E, Jäger F, Maier J, Ommer B, Kachelrieß M.
Eulig E, Ommer B, Kachelrieß M.
Baader E, Klein L, Maier J, Sawall S, Kachelrieß M.
Sawall S, Baader E, Wolf J, Maier J, Schlemmer HP, Schönberg SO, Sechopoulos I, Kachelrieß M.
Liu C, Klein L, Huang Y, Baader E, Lell M, Kachelrieß M, Maier A.
Duan L, Eulig E, Knaup M, Adamus R, Lell M, Kachelrieß M.
Sawall S, Maier J, Sen S, Gehrig H, Kim TS, Schlemmer HP, Schönberg SO, Kachelrieß M, Rütters M.
Conference Contributions
2025 EPCCT | iCT | SPIE | ECR | ESTRO | Fully3D | AAPM
2024 iCT | SPIE | ECR | RöKo | AAPM | CT Meeting | DGMP/ECMP | MIC | RSNA
2023 ESMPE | ECR | Pichl | RöKo | Fully3D | DGMP | ESMPE | MIC | RSNA
2022 SPIE | ECR | DSMF | BHPA | ESTRO | RöKo | CT Meeting | ECMP | RSNA
2021 ECR | NACP | RöKo | ECMP | Fully3D | AAPM | DGMP | MIC | RSNA | AFOMP
2020 iCT | SPIE | ECR | EMIM | ESTRO | AAPM | CT Meeting | DGMP | EANM | RSNA
2019 BASP | SPIE | ECR | ESTRO | ISMRM | CARAT | RöKo | Fully3D | AAPM | DGMP | RSNA
2018 Garmisch | iCT | SPIE | ECR | Pichl | CT Meeting | ISMRM | ECMP | DGMP | MIC | RSNA
2017 SPIE | ECR | RöKo | Fully3D | EANM | MIC | RSNA
2016 iCT | SPIE | ECR | Pichl | ESTRO | ISMRM | PSMR | CT Meeting | WMIC | MIC | RSNA
2015 Lorentz | SPIE | ECR | Pichl | ESTRO | RöKo | PSMR | Fully3D | ISMRM | RSNA
2014 SPIE | ECR | Pichl | ESTRO | RöKo | EMIM | CT Meeting | MIC | RSNA
2013 VSRN | SPIE | ECR | RöKo | Fully3D | APT | ICTMS | DGMP | MoBi | RTSD | RSNA
2012 SPIE | ECR | Pichl | RöKo | SCCT | iCT | CT Meeting | MIC | RSNA
Jobs
Are you interested in x-ray computed tomography (CT) and its manifold applications in medicine and other domains? Are you attracted by basic and translational research in these areas? Would you like to join our team for your master's thesis, diploma thesis, PhD thesis or postdoctoral activities?
Just contact Marc Kachelrieß and find out about possible options. We are happy to welcome you!
Get in touch with us
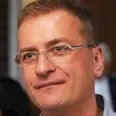